Wave Picking y Batch Picking, ¿Cuál es mejor para tus operaciones logísticas?
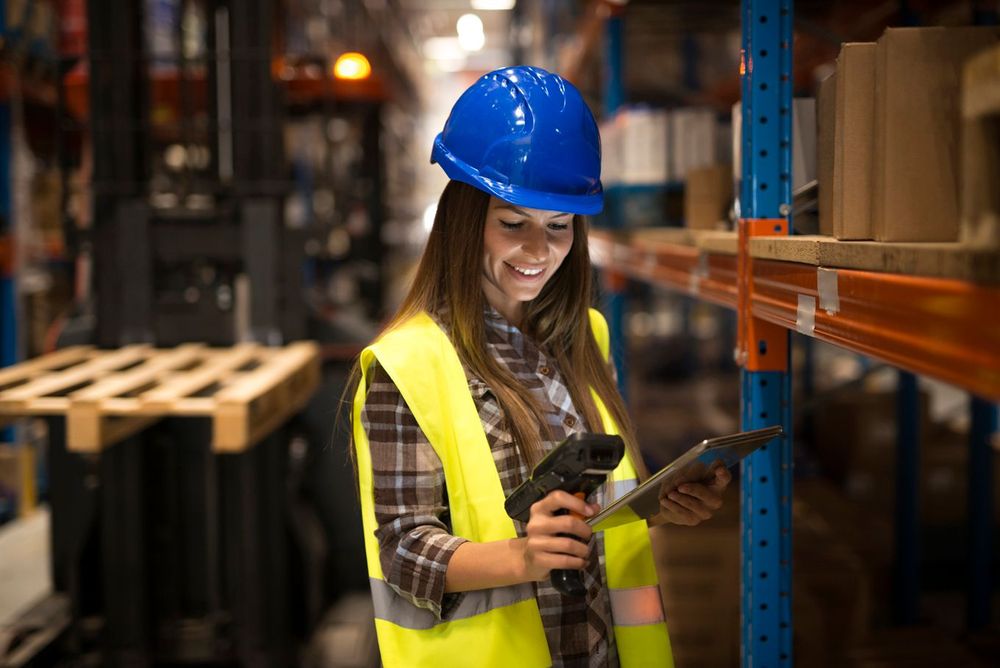
En otras entregas del blog hemos hablado de la importancia y el valor del picking en la cadena de suministro, debido a esto se han desarrollado varias formas de hacerlo más eficiente con la finalidad de contribuir a un mejor desempeño de las operaciones, hoy vamos a hablar de dos métodos de picking, wave picking o picking por oleadas y batch picking o picking por lotes, que aunque comparten algunas similitudes cumplen funciones específicas y completamente diferentes aunque algunas veces pueden confundirlas.
El wave picking o picking en olas u oleadas es un método que consiste en agrupar pedidos que comparten un criterio en común como por ejemplo cliente, fecha de entrega, ruta de transporte, transporte asignado, entre otros y se preparan en un determinado periodo de tiempo agilizando de esta forma la preparación de los pedidos ya que en una jornada laboral se pueden programar varias oleadas, para que este método funcione a la perfección es necesario el uso de un sistema de gestión de almacenes (SGA /WMS) ya que el sistema se encargará de programar la oleada y la ruta de picking para hacerla más rápida y eficiente.
¿Cuándo conviene poner en práctica el wave picking?
Este método es ideal si:
El tipo de picking implementado en el almacén es man to goods u hombre a producto.
Si el almacén cuenta con un sistema de gestión de almacenes SGA.
Si el almacén alberga un número considerable de referencias o SKU.
Aún si se cumplen estos requisitos es necesario evaluarlo con detenimiento antes de ponerlo en marcha, e inclusive hacer pruebas pilotos para corroborar si este método es el que se adapta mejor al tipo de operación de tu almacén.
Beneficios de implementar el wave picking
La aplicación del wave picking puede traer muchos beneficios a tus operaciones entre los que podemos mencionar:
Optimización del tiempo: con la aplicación del WP se reducen considerablemente los tiempos de preparación de los pedidos ya que el tiempo invertido en el picking es menor, además se procesan más pedidos en un mismo período de tiempo.
Recorridos más cortos: al estar las rutas planificadas por un SGA los recorridos serán más cortos y precisos, además como se procesan varios pedidos al mismo tiempo se evita el constante ir y venir que implica preparar un pedido a la vez por lo tanto se agiliza considerablemente el proceso.
Mejora el flujo de stock: al aplicar este método con la ayuda del SGA tendrás un control total del flujo de productos del almacén lo que te permitirá planificar las reposiciones y evitar los quiebres de stock.
Maximiza el proceso de recolección: la aplicación de este método permite recoger más productos por viaje que otros métodos, lo que lleva a tope la capacidad de recolección y por lo tanto de manejo de pedidos al mismo tiempo.
Batch Picking o picking por lotes
El Batch picking o picking por lotes es un método que consiste en recoger en un mismo recorrido varias unidades de un mismo producto que forman parte de pedidos diferentes, para luego distribuirlos en el área de empaque facilitando la preparación masiva de pedidos, en este caso a cada operario se le asigna un producto específico y un grupo de pedidos para hacerlo más eficiente, al igual que en el caso del wave picking es necesario el uso de un sistema de gestión de inventario que se encargará de agrupar los pedidos, asignar el producto a buscar, diseñar la ruta para luego asignarlo a un operario, en este caso a cada operario le corresponde un producto o un mismo operario puede hacer tantos viajes como productos tenga asignados eso sí debe recopilarlos un modelo o SKU a la vez.
Tipos de batch picking (BP) o piking de lotes
Aunque la principal premisa de este tipo de picking es la recolección de productos con una misma referencia o SKU, existen varias formas de ejecutarlo y son la siguientes:
BP tradicional: aquí los productos recogidos, son depositados en un carro para luego ser divididos y consolidados en el área de preparación de pedidos, el beneficio de esta técnica es que al no implicar ningún tipo de clasificación se pueden tomar más unidades del producto por viaje y el proceso es más rápido que las otras modalidades.
BP Pick to cart o picking con carros: es un tipo de picking en el que el operario usa un carro que lleva a lo largo de los pasillo del almacén en busca del producto asignado, cada carro cuenta con gavetas plásticas que corresponden a un pedido en particular, así que al momento de la recolección del producto el operario ejecuta las labores de consolidación, facilitando el proceso de empaque.
BP pick to box: esta es la técnica más compleja pues como su nombre lo indica el operario deberá llevar en su carro las cajas que corresponden a cada pedido, así que al momento de hacer la recolección también llevará a cabo las labores de consolidación y empaque, lo que requiere de gran conocimiento de los productos ya que se debe considerar con anticipación el volumen que cada pedido ocupará para poder escoger la caja que corresponda.
¿Cuándo conviene poner en práctica el batch picking?
Este método es ideal si:
-
Se manejan muchos pedidos con una misma referencia.
-
Si el almacén maneja un número limitado de referencias.
-
Si el almacén cuenta con un sistema de gestión de almacenes SGA.
-
Si la dimensión y peso de los productos permite el traslado de un número considerable de piezas pues evidentemente un pedido de hornos tostadores requerirá más espacio y esfuerzo para trasladarlo que un pedido de collares.
Al igual que con el wave picking es necesario evaluar con detenimiento si este es el método que mejor se adapta a la operaciones de tu almacén y hacer algunas pruebas antes de implementarlo.
Beneficios de implementar el batch picking
La aplicación del batch picking puede traer muchos beneficios a tus operaciones entre los que podemos mencionar:
Ahorro de tiempo: al igual que el wave picking este método permite procesar muchos pedidos al mismo tiempo pero como el proceso de recogida es de un solo producto, si el tamaño y peso lo permiten se pueden procesar más productos por recorrido.
Reducción de distancias recorridas: gracias al uso del SGA se optimizan los recorridos y los operarios pueden trabajar por zonas asignadas dentro del almacén, lo que facilita y agiliza el proceso de recogida de productos.
Reducción de errores: como cada operario se dedica exclusivamente a recoger un producto específico por viaje se reduce considerablemente el margen de errores.
Agiliza el proceso: en los casos que se aplica el pick to box no solo se está llevando a cabo la recogida del producto si no que en cada viaje se consolida y se empaca el pedido lo que hace mucho más eficiente y rápido el proceso de picking.
Como has podido ver ambos métodos son eficientes y definitivamente contribuirán a la optimización de tu proceso de picking pero, sin importar cual elijas para que funcionen eficientemente, necesitas de un sistema de gestión de almacenes (SGA/ WMS), un buen diseño de layout de almacén que contribuya a agilizar el proceso de picking, llevar a cabo un período de prueba para evaluar si el método que quieres implementar es el ideal para tus operaciones, pues que sea bueno y efectivo para otras empresas no quiere decir que sea beneficioso para la tuya, así que ponerlo a prueba antes de dar el paso a una implementación completa es lo más recomendable y ser por supuesto flexibles en todo el proceso de evaluación previa a la implementación, iterar entre entre ambos métodos y corroborar cual es el que aporta más beneficios a tus operaciones contribuirá a un proceso de implementación más fluido y eficiente.
Si necesitas asesoría sobre los sistemas y la tecnología a implementar en tu empresa en Symlab podemos ayudarte ya que somo expertos en software personalizado de logística y transformación digital agenda una llamada con nosotros hoy info@symlab.io